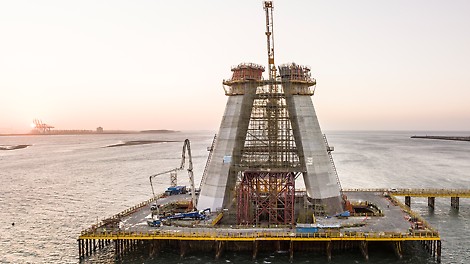
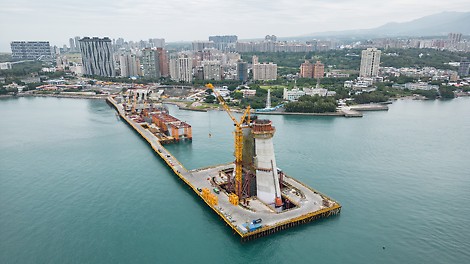
Download Press Release
The images in more detail
The following is an overview of the images contained in the press set.
The pier of the bridge rises 200.00 metres above the water surface of the river and required detailed planning in compliance with strict safety guidelines. PERI is assisting with the project by providing individually planned and coordinated formwork and engineering solutions to ensure that the unusual pier design can be constructed on schedule.
An architectural artwork connecting road traffic to the Bali District
Zaha Hadid won the Danjiang Bridge International Competition back in 2015 for her design of the asymmetrical bridge. Once completed, the bridge will connect Tamsui District in New Taipei City with the Bali District across the river – thus relieving the pressure on other transport routes. In addition, the Danjiang Bridge will become a new, unmistakable landmark of the city.
The pylon in the centre of the bridge is the real eye-catcher. It towers into the air in the shape of an upturned “Y” and stands, figuratively speaking, with its two legs in the river. The stay cables, which run in parallel to the top of the pylon from both sides, give the structure a futuristic appearance.
PERI was involved in the construction of the pylon by providing, among other things, a custom-designed formwork solution for concreting a total area of 18,000 m². To create this futuristic look, PERI developed a freeform formwork system specifically for the project to construct 3,000 m² of the entire surface. The complex, ever-changing shape of the pylon, which stretches upwards over 53 sections, posed the biggest challenge. PERI provided versatile VARIO, SCS and ACS, which could be individually adapted to the varying geometry.
Everything from a single source: Catering for specific requirements using PERI Systems
PERI Systems are characterised in particular by their adaptability to unusual project requirements as well as their compatibility with other PERI products. Using PERI’s standard portfolio as a basis, the engineers from PERI came up with a coordinated, customised solution from a single source for each section of the unique pylon shape.
As such, the VARIO GT 24 Girder Wall Formwork provided the ideal foundation for each section of the 200-metre-high pylon. After all, this dimensionally stable formwork makes it possible to pour up to 18 metres of concrete at a time.
Hitting the heights safely and quickly with PERI Climbing Systems
To realise the various shapes and radii of the pylon, PERI Climbing Systems were used alongside formwork solutions. A combination of ACS and SCS was chosen to ensure that processes were quick and efficient. The SCS Climbing System made it possible to construct the inclined design at the upper and lower ends. To help construct the central, straight section, the ACS Self-Climbing System was used, which climbs up the emerging building on rails.
“Since we have been using PERI products, the project has been running smoothly. The efficiency is constantly high so that our requirements regarding the progress of the projects are fully fulfilled. For us, it is a good feeling to know that PERI is always able to competently solve any problems that arise during the entire construction process. We are very satisfied with PERI’s service because it enables us to work efficiently.“
Zeng Wei-Cheng, Site Manager, KSECO
Project support during construction
PERI engineers are on hand to advise the construction site team throughout the project. From start to finish, the experts provide support with planning and preparation, on-site construction and final completion. The intensive, detailed planning process and on-site support has ensured rapid construction progress. This enables the project requirements to be met and the tight construction schedule to be adhered to. In this way, the project requirements can be met in order to get closer to the planned completion date of 2025 day by day.
About PERI:
With sales of € 1,846 million in 2022, PERI is one of the leading manufacturers and suppliers of formwork and scaffolding systems. With a workforce of around 9,100 employees and well over 160 warehouse locations in more than 70 countries, the family-owned company with its headquarters in Weissenhorn (Germany) provides its customers with innovative system equipment and comprehensive services relating to all aspects of formwork and scaffolding technology.
Contact persons
If you have any further questions about text or image material, please contact our press department directly.
-
-
Tanja HäuptleTrade Media
-