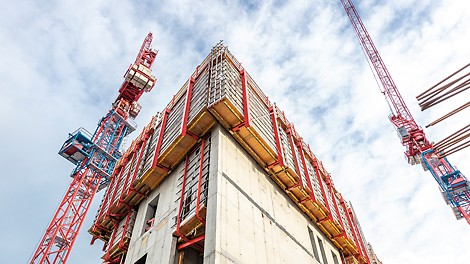

Download Press Release
The images in more detail
One of the major technical challenges during the construction of the new tower was the cantilever at a height of around 125 m: The engineers from PERI designed a project-specific support structure consisting of climbing rails from the RCS Rail Climbing System as well as components from the VARIOKIT Engineering Construction Kit and the PERI UP Scaffolding Kit.
Trailing wall formwork for complex building core
A key feature of the overall project was the large, compartmentalised building core with its constantly evolving cross-section. The two self-climbing systems ACS P and ACS G were used during construction together with trailing wall formwork. These provided additional storage space when working at height. Furthermore, the gallows of the ACS G could be optimally adapted to the complex structural conditions. The RCS Rail Climbing System was used on the front sides. The repositioning units, which were firmly connected to the structure at all times by means of climbing shoes, made it possible to climb upwards safely without the need for a crane. The climbing solution also impressed with its ability to adapt easily to the various structural conditions – without compromising on speed and work safety.
Core elements of the support structure
To construct the triangular cantilever on the 33rd floor, the engineers from PERI developed a special construction: 14 console brackets were produced using RCS Climbing Rails as a basis. Within the support brackets, the bracing was carried out using VST Horizontal Ledgers and VST Diagonals. The nodes were joined together with the aid of special connectors. Due to the confined spatial conditions at the inner-city construction site, each of the console brackets had to be pre-assembled in seven transport units at the PERI warehouse in Bürstadt and the PERI formwork assembly facilities in Weissenhorn.
Safe working conditions even at great heights
On arrival at the construction site, the 14 console brackets underwent final assembly on the ground and were lifted by crane to a height of 125 m for anchoring. The resulting loads were transferred via tension rods into the slab of the 31st floor and the base plate of the 29th floor. A separate access scaffold was erected to provide safe access for site personnel so they could assemble and disassemble the units. Two girder grids were fixed to the top chords of the support units as load distribution and working levels on which the shoring and working scaffold was later erected using components from the PERI UP Scaffolding Kit. The head spindles of the PERI UP falsework supported the actual slab formwork with an integrated edge beam.
A successful project using tailored system combinations from a single source
By combining PERI standard systems with tailored system solutions, it was possible to deliver a custom-fit solution that met all of the specific requirements of the major project. The optimised interplay of these single-source systems also meant that the regular floors could be realised in a weekly cycle. As a result, it was possible to adhere to the tight construction schedule – the project was completed on time in July 2022.