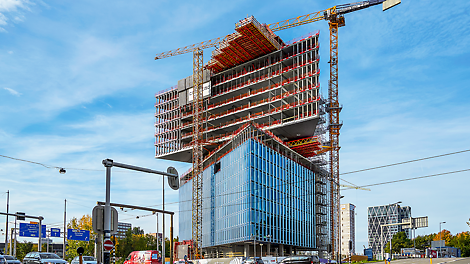
Amsterdam is one of the most popular destinations in Europe. The NH Hotel Group recognised the high attraction of the Dutch capital and had the nhow Amsterdam RAI Hotel built not far from the city centre. With its 91 meters and 650 rooms, it is now one of the highest accommodation establishments in the Benelux and has been an iconic landmark of the Amsterdam skyline since its completion in 2019. It was designed by the two renowned Dutch architects Rem Koolhaas and Reinier de Graaf, who are known for their modern designs.
In order for the striking building with its complex triangular structure to be built at all, client-specific formwork solutions were required that had to be efficient and safe to use as well as meet the specified budget and tight schedule. In addition, our client RED Bouw wanted to pour the entire concrete structure of the hotel, with the exception of the stairs and platforms on site, so it needed an efficient formwork solution. This makes them one of the few Dutch construction companies that still rely on on-site concrete. RED Bouw was therefore looking for a partner who could cope smoothly with the strict requirements.
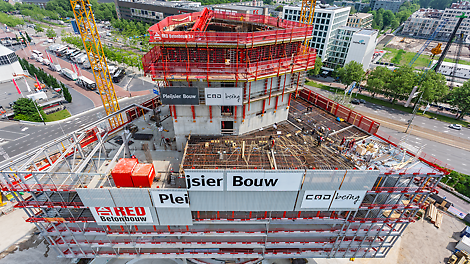
Phase 1: Convince with a good offer and teamwork
In order to meet all requirements, our branch in Schijndel worked meticulously to support our clients with the right formwork and scaffolding systems during construction. For the protrusions in the 10th and 17th floor, the team worked closely with the engineers at PERI Headquarters in Germany to satisfy the safety aspects. Among other things, Martin Fischer was responsible for the formwork concept of the six cantilevers. His colleague Andreas Hauber dealt with the topic of climbing formwork. While the two engineers worked out the formwork designs, our Dutch team was on site in Amsterdam and in direct exchange with our client.
Due to the lack of space, RED Bouw wanted to do without a supporting scaffolding and start work on the façade a few floors down. "Here it was important to us to advise our clients in the best possible way so that there were no surprises on the construction site," says Andreas, adding: "We have therefore developed suitable solutions that are cost-efficient and meet the specified schedule and the wishes of our clients. This was ultimately the decisive reason why RED Bouw decided to realise the modern hotel together with us.
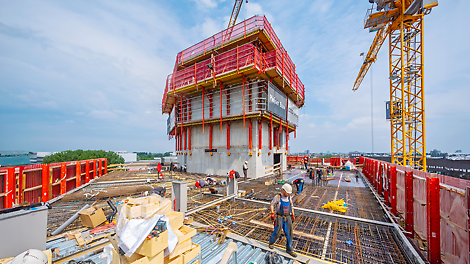
Phase 2: Optimal construction site organisation on site
Efficiency was the central theme in the construction of the building core. Because: Within eight days, a floor was to be concreted, which was very ambitious due to the complex geometry. To achieve this goal, our climbing formwork was used. Andreas knows them down to the smallest detail and was on site to advise RED Bouw with his expertise. "In order to pour the concrete efficiently, the core had to be divided into different segments and the work on the building had to be rectified. That is, one part of the construction team only worked on the walls, another team exclusively on the ceilings. I advised and assisted our customer, so that he knew where the core should be separated," says Andreas.
Since our RCS self-climbing system includes its own, large-area work plane, the walls could be built floor by floor in combination with our MAXIMO wall formwork, regardless of the ceiling work. Here, too, Andreas was on hand to determine which formwork should remain in place and which should be retracted. "All these aspects have a major influence on the further course of construction. Changing the sequence of processes can cause major delays. That’s why we’re on site during the decisive phase, so that everything runs smoothly," says Andreas. Our SKYDECK formwork was used for the ceilings, which, with its handy and lightweight system components, enables energy-saving work and short formwork times. This allowed the teams to work flexibly at different levels and to comply with the customer's specifications.
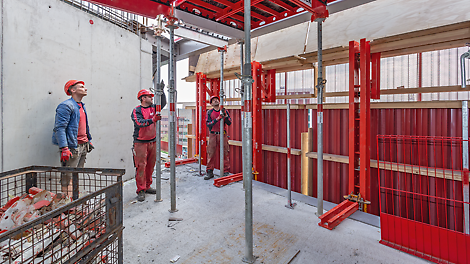
Phase 3: Mastering safety, deformation and disassembly at high altitudes
With increasing height, new challenges were added. But our systems and the solutions of our engineers ensured a smooth implementation. For example, the safety of workers, which was a top priority at all times. Since our climbing formwork offers a seamless working level as well as fall protection and was directly connected to the hotel, the climbing process was safe for the entire team. Our systems were assembled and disassembled just as safe. Martin was particularly in demand here. "Since the superstructure created by the cantilever was not yet available at the time of assembly, our formwork could easily be mounted with the crane," he says and adds: "It looked different during disassembly. The superstructure was present here, so that the materials could not be easily dismantled. The solution was therefore to let our cantilevered VRB heavy-duty truss girder climb horizontally into the interior of the building. This made it possible to dismantle the superstructure and safely dismantle the formwork at a suitable location."
In addition to the safety aspect, our engineers could not ignore another important issue: the deformation of our formwork during cantilevers. "It is normal, as large concrete loads push down on our formwork systems. But here, the devil is in the detail. In order to keep the deformations to a minimum, we had to accurately calculate the loads acting on our formwork. Based on the data, we used additional components from our PERI UP construction kit and integrated them into our formwork. These helped to remove the loads and compensate for the deformation," says Martin. In addition, tests were conducted prior to deployment to confirm Martin's calculations.
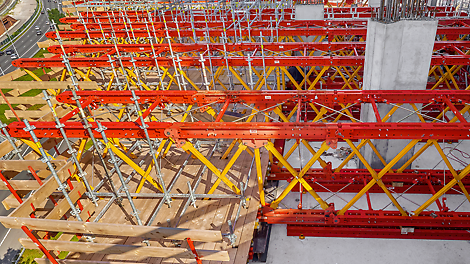
Phase 4: An inspiring innovative and efficient solution
The biggest challenge for our engineers were probably in the 10th and 17th floors: the cantilevers. Since a load-bearing framework from the floor to the cantilevers would not have been efficient, our engineers had to think outside the box and find a unique solution that would make the 12.5-metre-long superstructure possible in an efficient way. So Martin and his team decided on a completely new solution: "We tried many things, but in the end we came up with the idea of using our VRB heavy-duty truss girder. In this way, we both ensured a safe working platform and created a supporting structure that offered space for the material." The special feature of this is that the heavy-duty truss girder is usually used in bridge construction and is inclined to the left or right. With the nhow Amsterdam RAI Hotel, however, it was used for the first time in a high-rise project and was used here as a cantilever. "This is what made the project so unique and forward-looking," Martin emphasises.
This solution impressed the industry so much that construction companies such as PCL Construction Management travelled to the Netherlands to see the heavy-duty truss girder in action. For the construction of the Calgary Cancer Centre in Canada, they were also looking for an efficient method of cantilevering. After all, we were not only awarded this contract, but also follow-up projects with other construction companies that presented similar challenges. "Our client RED Bouw was sceptical at first, but we were able to convince them of our solution. And in the end, they were not only satisfied, but enthusiastic about the result. There could not have been a better happy ending for us," says Martin.
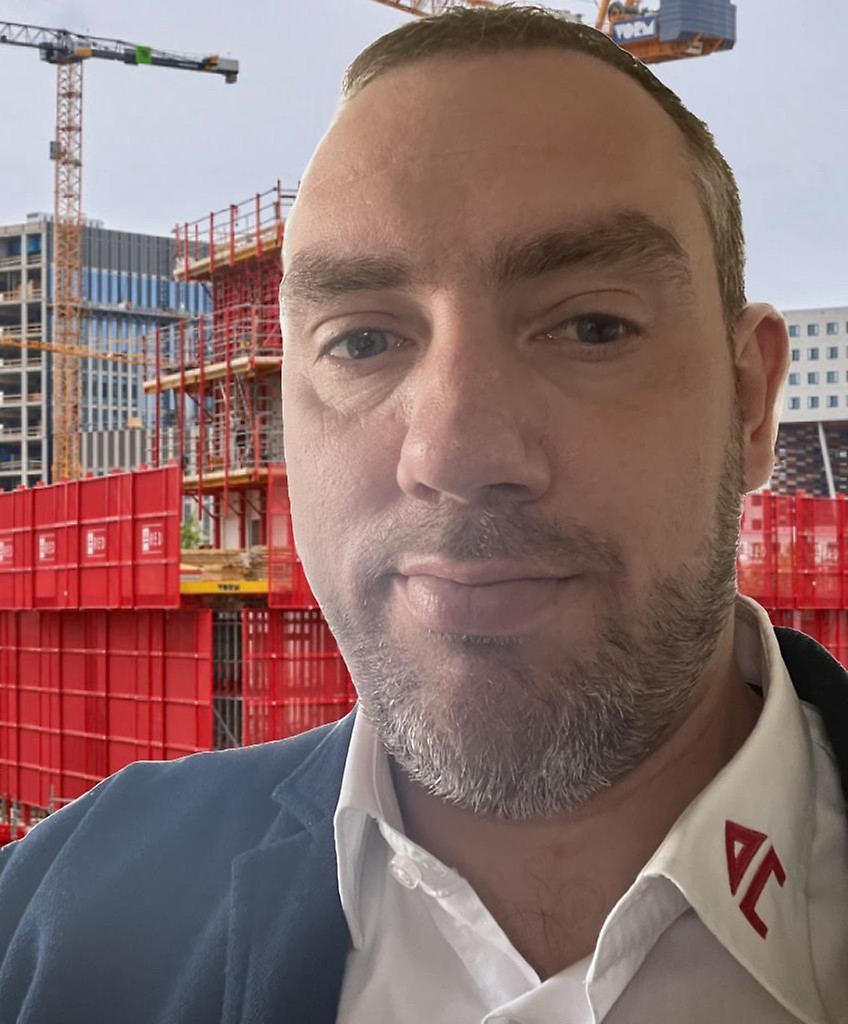
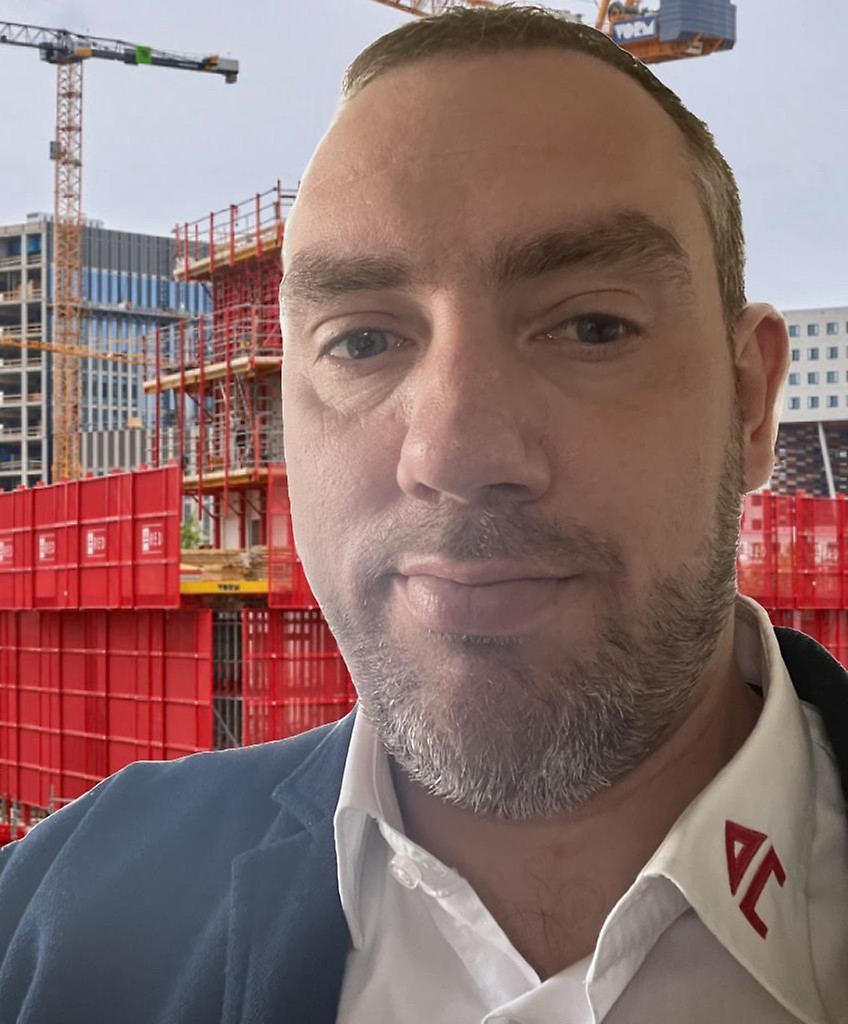
We are on site for you worldwide
Our support knows no borders - no matter where you are in the world. Simply select the website for your country and discover detailed information about our products, projects and contact details for our local contacts. We are always happy to assist you and look forward to helping you too.