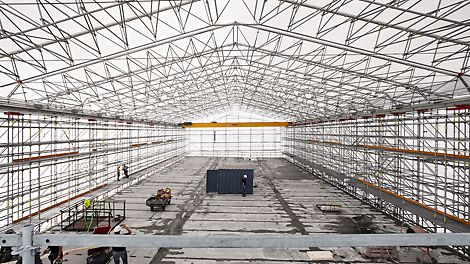
Since joining PERI in 2007, Anna has quickly developed into an expert in scaffolding construction. Since then, she has not only contributed her knowledge, but also her passion for inspiring others in this field. ‘I love demonstrating the added value of our PERI UP scaffolding system,’ she says. That’s why she shares her know-how within the company by regularly training new colleagues and supports scaffolders with complex projects, making her one of the first addresses when questions about scaffolding statics arise. ‘Structural engineers are often seen as lone wolves, but in reality, we are present on construction sites and speak directly with our clients,’ she says enthusiastically. This close collaboration enables her to precisely understand the daily requirements of scaffolders and develop customised solutions.
A formative project and a prime example of Anna's practical expertise was the building enclosure in Falkenberg, Sweden. It was one of her first major international projects, which she supported right from the start. The challenge: the construction team had to withstand snow and strong winds throughout the winter months. Our PERI UP Flex Weather Protection Roof was therefore used during the construction phase. As the total area of the enclosure was larger than usual, additional push-pull props were required to give the scaffolding the necessary stability and to absorb the high wind loads on the side walls. ‘This meant that the work could be carried out safely on site, regardless of the weather,’ recalls Anna.
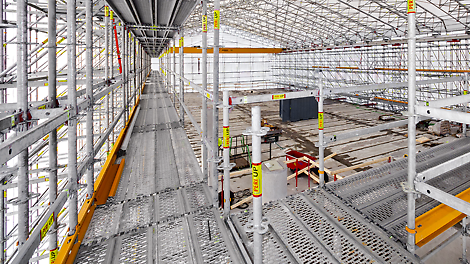
Efficiently combining our scaffolding and engineering kit for small construction sites
Things got particularly interesting when a large crane could not be used due to the enclosure – a mobile solution was needed in form of an internal crane runway that could run on the scaffolding. ‘This meant that, in addition to our enclosure system, we also required a joint working and shoring scaffold which could take the loads from the crane, provide working surfaces and be safe and stable at the same time,’ explains Anna. By combining our PERI UP Scaffolding Kit with our VARIOKIT Engineering Construction Kit, she developed a solution that united stability, flexibility and safety. RCS Climbing Rails were used to transfer the high vertical loads from the gantry crane while SRU Steel Walers transferred the load to the scaffolding system, demonstrating the effective interaction between the two modular systems.
‘Thanks to this compatibility, we can react flexibly to the needs of the scaffolders and reduce the assembly effort,’ says Anna.
But she's not the only one who is impressed by our systems; the construction company Tage & Söner was also very pleased. The positive feedback was reflected in their decision to buy all the material. ‘This is a nice confirmation of our work,’ says Anna.
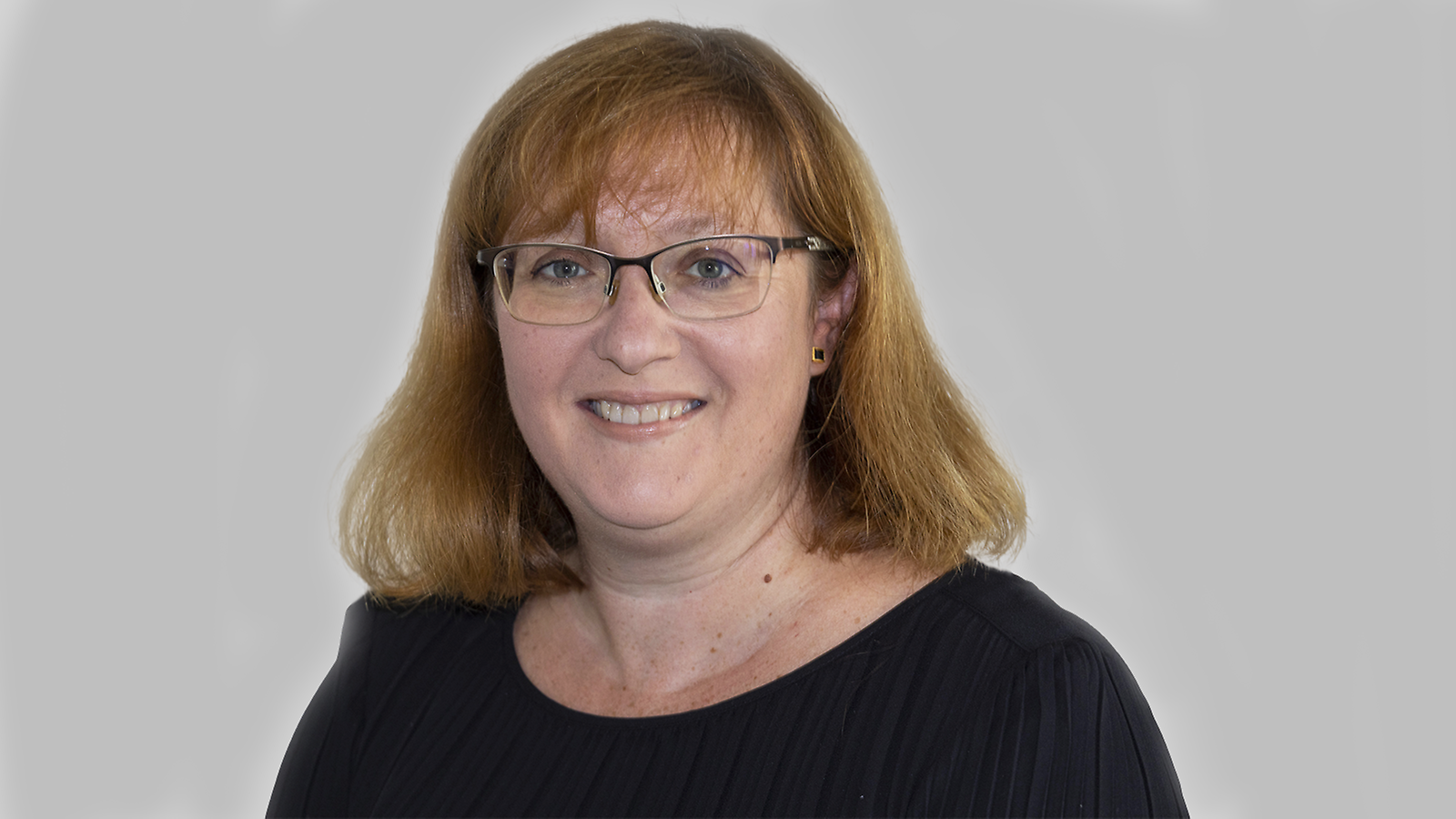
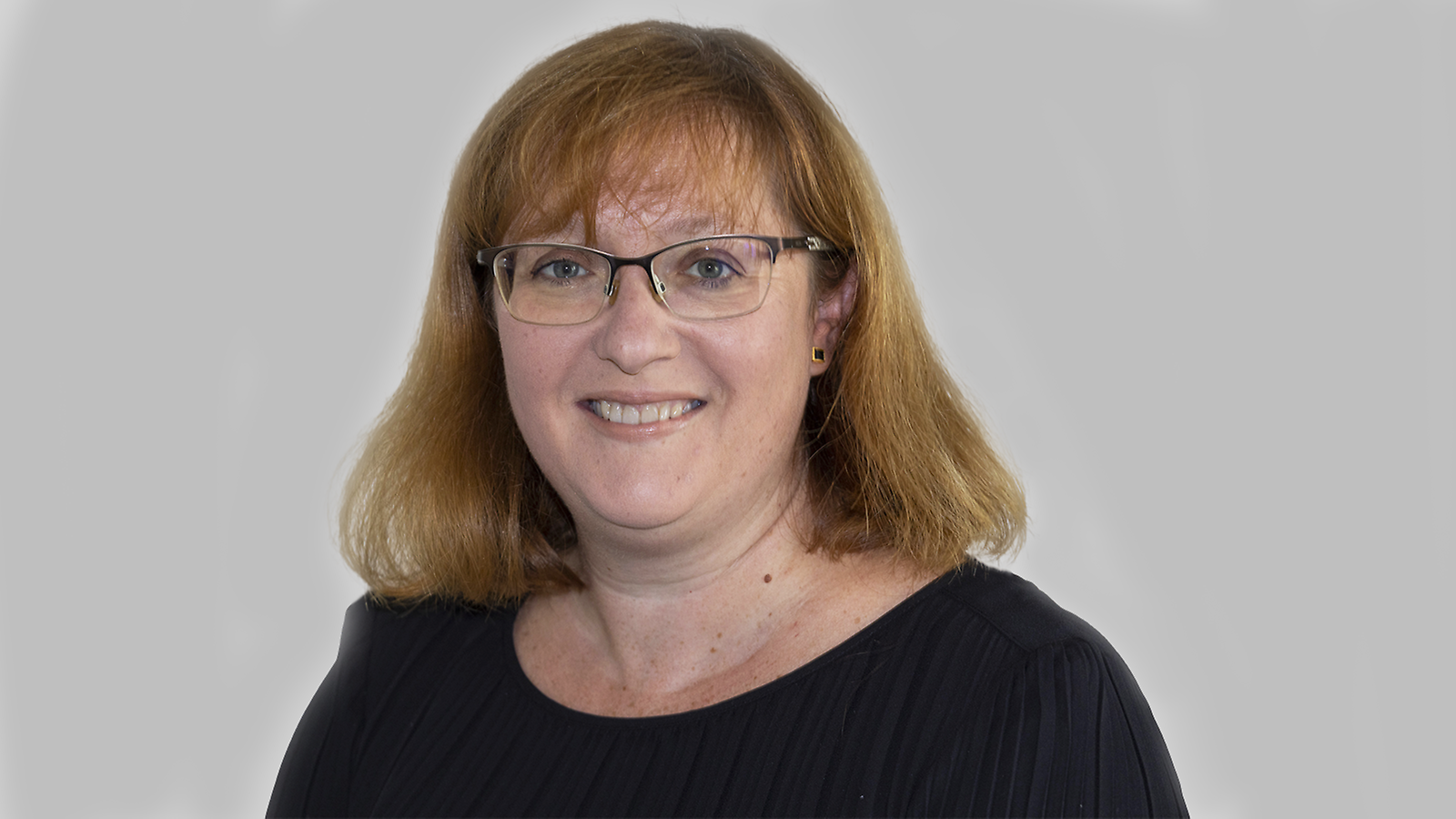
From tarpaulin to innovative enclosure: How Anna is driving the further development of our products
While a conventional protective tarpaulin was previously used in Falkenberg to enclose the structure, this solution has evolved in recent years. Anna knows why: ‘As the desire for a more robust system came up more and more often in discussions, we took a new look at our enclosure.’ In this regard, Anna forms the bridge between the scaffolders and our product development team and is one of the driving forces behind the further development of the Scaffolding Construction Kit. ‘I'm pleased that I can contribute my practical project experience internally and provide valuable feedback,’ says Anna.
This is how the innovative PERI UP Cladding was developed as a ready-made solution. The enclosure system made of resistant polycarbonate is flame-retardant and can be installed easily and directly on the scaffolding thanks to fewer components. The lightweight design not only supports ergonomic working, but also enables assembly from a secure position. In addition, the enclosure provides sufficient light and offers the construction site team reliable protection from all weather conditions. Passers-by also benefit from the solution, as they are shielded from dust, dirt and noise.
‘The PERI UP Cladding should therefore make the assembly work for the scaffolders noticeably easier. This includes introducing them to our further development and showing them the advantages of the system,’ says Anna.
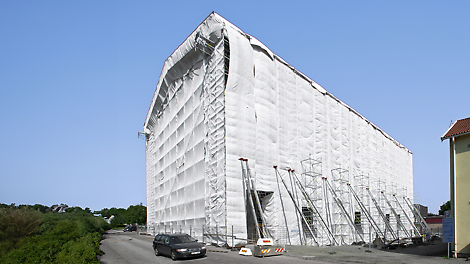
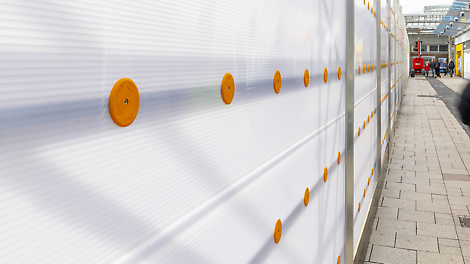
Focusing on client needs: Anna's instinct for future challenges
The PERI UP Cladding was not the only further development that has advanced scaffolding construction. Anna's talent for recognising client needs at an early stage and developing solutions even before the scaffolders formulate their requirements was also demonstrated at the 2012 Olympic Games in London. For the construction of the beach volleyball court substructure, Anna worked with the product development team to design a handy system formwork girder. From discussions with a scaffolding company, she knew that the system-free versions were large and unwieldy and took up a lot of space. So, Anna and her colleagues investigated how this system could be made smaller. This resulted in our PERI UP Formwork Girder ULS Flex. Individual components with a length of up to 1.50 metres and a maximum weight of 15.4 kilograms, the girder is now significantly smaller and lighter than its alternative and can be erected even faster. ‘This saves the assembly team valuable time and ensures a stable and closed surface even in cramped working conditions in combination with our PERI UP Flex Covers’ she explains.
In the end, the beach volleyball players celebrated gold at the Olympic Games. The project remains in Anna's memory not only because of this success, but also due to the fact that the formwork girder has established itself as a standard and is still used by many scaffolders today. For example, the Würth branch was successfully remodelled with this system – while the business continued to operate. ‘It's always nice to see how a small conversation can result in a product that proves itself on the market and continues to inspire years later,’ says Anna satisfied.
We are on site for you worldwide
Our support knows no borders - no matter where you are in the world. Simply select the website for your country and discover detailed information about our products, projects and contact details for our local contacts. We are always happy to assist you and look forward to helping you too.