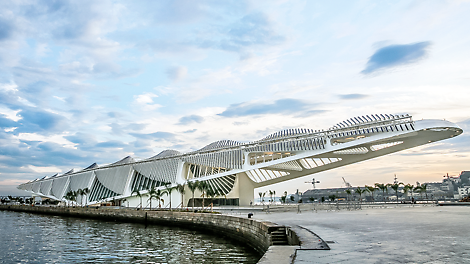
In the Free-Form Concrete Team, David can realise exactly the projects he is passionate about. Here, everything revolves around the planning of extraordinary special formwork projects – from the impressive domed roof of the Indoor Tennis Center in Kuwait to the expansion of the largest cultural centre in Washington D.C., the John F. Kennedy Center. The more unusual the construction projects, the more exciting they are for David. "I need a challenge every day that fulfils me in my work," he says.
The Museum of Tomorrow in Rio de Janeiro has a very special place in his heart. "It was my first major project – and such a complex one that required not only me to familiarise myself with the new tasks, but everyone involved," says David. The Spanish architect and engineer Santiago Calatrava was striving for uniqueness and wanted to make the Museum of Tomorrow on Rio de Janeiro's old harbour the new landmark of the Brazilian metropolis. The project was accordingly unique as the futuristic building on a pier was to stretch 300 metres into the sea like a giant tongue and be ventilated through movable façades and roof openings. On an area of 5,000 square metres, curved walls, round viewing platforms and an exhibition wing with two floors connected by sloping ramps had to be planned extremely precisely and well. The aim was to complete the museum in time for the 2016 Olympic Games, so the project was on a tight schedule and budget.
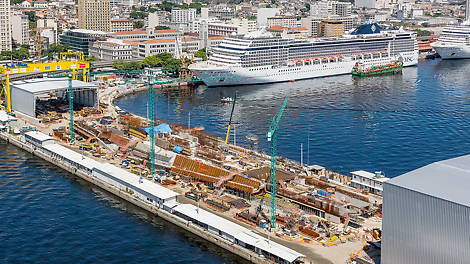
When passion shapes the planning
Not an easy task for David and the entire formwork team. Even back then, our engineer realised that unusual construction projects are exactly the kind of projects that drive him in his daily work. "I love the time when you have to deal with a building for the first time and develop a formwork concept. That's the most creative phase for me, when I can really express myself and get wild with my ideas," says David.
This passion played a key role in the planning of the museum and drove him to peak performance when faced with tricky tasks. For example, the curved shape of the viewing platform presented a major challenge. "Our formwork stood on our PERI UP shoring. We knew that several tonnes of concrete would be poured into our formwork and that the forces would press into our scaffolding and thus compress the walls. We had to take this change in shape into account during planning so that the platform would have the desired shape after the concrete had been poured," says David.
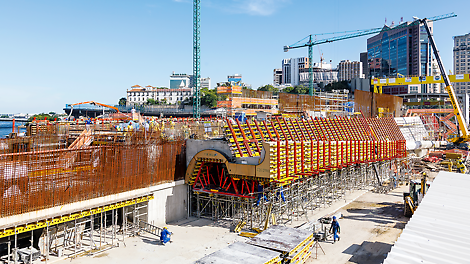
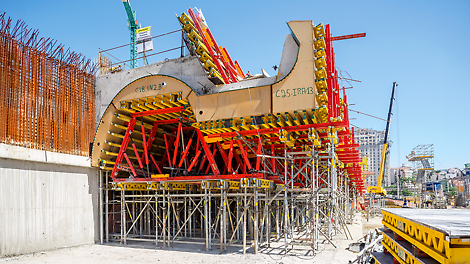
Our recipe for success: expertise, teamwork and efficiency
When our expert is looking for solutions like these, he usually shares ideas with colleagues and receives new inspiration. "The intensive exchange within the team is enormously important to find the perfect solution for our clients together. This is extremely valuable and something I really appreciate at PERI," says David.
Almost twenty PERI engineers pulled together and planned, manufactured and delivered over 3,500 customised special formwork elements in just thirteen months. While the complex 3D free-form surfaces were carefully developed in Germany, the formwork assembly took place in the branch office in São Paulo, Brazil. Prefabrication was the key here. The 3D formwork elements were produced there and then transported to Rio de Janeiro. "This not only saved us costs, but also an enormous amount of time," says David.
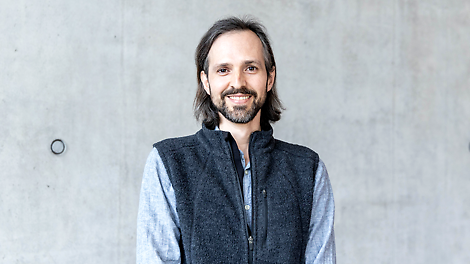
"When changes occur on the construction site at short notice, you initially think the world is coming to an end and the new situation is unsolvable. But then you always find a solution together in a team."
David Dittmann
Senior Project Engineer
Always keeping an eye on the future
David’s job doesn't just involve planning customised formwork. Our expert also travels around the world to work on the buildings of the future. "At the Museum of Tomorrow, I rotated with a colleague from time to time for a year so that we could get a better overview of the requirements," says David.
Now that the pioneering museum has been completed for several years, we took the opportunity to ask David how can such complex construction projects be built in the future? This is where our engineer let his imagination run wild. What if VR glasses had already become established on construction sites? What if tomorrow you could put yourself on top of the museum and scale the dimensions of the building with a finger zoom? What if engineers could use artificial intelligence to develop and construct customised formwork solutions even faster? Or if entire swarms of drones could bring all the materials to the site like busy bees and transport as well as logistics would no longer play a major role?
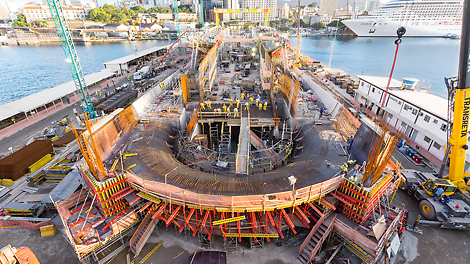
Many of these future visions are further along than you might think. For example, our expert sees 3D concrete printing as a key development that is already part of the construction industry: "3D printers are being used to build apartment blocks. If the technology develops as quickly as it has so far, 3D printing could also be used for particularly challenging buildings such as the Museum of Tomorrow in the near future," says David. This would make us even more flexible, efficient and cost-effective.
In the end, David is and remains a realist and believes: "Although the technologies are developing, we engineers will still have to be in charge in the future. A supervisor will always be needed as well as someone who has the expertise to choose the right solution or who thinks in all directions and is creative. Clients will continue to want high quality and efficient solutions in the future. With our ingenuity and intuition, we engineers will simply be indispensable for this – even in 30 years."
We are on site for you worldwide
Our support knows no borders - no matter where you are in the world. Simply select the website for your country and discover detailed information about our products, projects and contact details for our local contacts. We are always happy to assist you and look forward to helping you too.