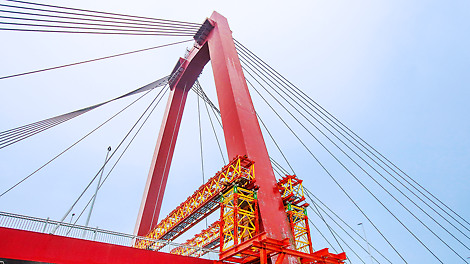
Martin has been part of our team since 2011. While he has specialised in bridge projects his particular focus is on shoring systems. These and many other PERI systems can be customised and combined with each other – for example, with the PERI UP scaffolding construction kit. What he loves most is the varied planning that some projects require. ‘Every construction site is unique. And that's why we always have to think outside the box and be creative. After all, we don't develop cars that are produced millions of times over,’ says Martin.
The renovation of the 356-metre-long Willems Bridge offered Martin plenty of scope for creative solutions and is therefore one of his favourite projects. The two striking red pylons that characterise the Rotterdam cityscape were to be repainted and coated one after the other. What looked like a simple task at first glance turned out to be a major challenge since the traffic had to continue to flow without interruption.
Our client, the construction company Steigerbouw van der Panne, therefore required a stable support structure on which our PERI UP scaffolding stood. The cable-stayed bridge was only closed for a few hours during the night in order to deliver and assemble the material. The safety of the workers and meeting the specified schedule were equally important requirements that Martin had to take into account in his concept and structural calculations. To ensure that the project remained efficient, there was also the need to minimise the use of materials.
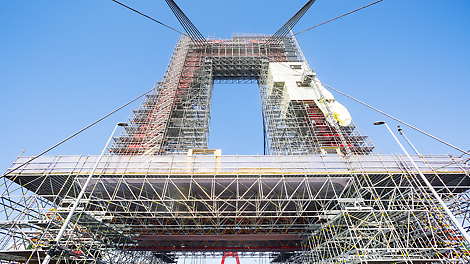
New approaches to bridge renovation: Heavy-duty truss girder as the key to success
In order to fulfil all the specifications, Martin worked closely with his colleague Tobias Elstner. Together, they came up with a suitable solution: a system mix of VST heavy-duty towers, VRB heavy-duty truss girders and special steel structures. One decisive aspect was the use of the truss girders – in a completely new role. The system, which is usually used for new bridge construction, was used for the first time in a renovation project. Due to its flexibility and high load-bearing capacity, it could form the roof of the supporting structure. With a length of around 40 metres, the truss girder covered the entire width of the road and withstood the high loads of around 200 tonnes of scaffolding material as well as the string winds.
However, this also resulted in a typical deformation. In such cases, a well thought-out solution is required right from the start in order not to delay the project.
Martin therefore developed a suitable customised steel structure that provided a straight surface on which both the heavy-duty towers and the truss girders could be safely positioned. ‘As this solution has proven its worth, we have used it several times for bridge renovations since then - always to the satisfaction of our clients,’ says Martin.
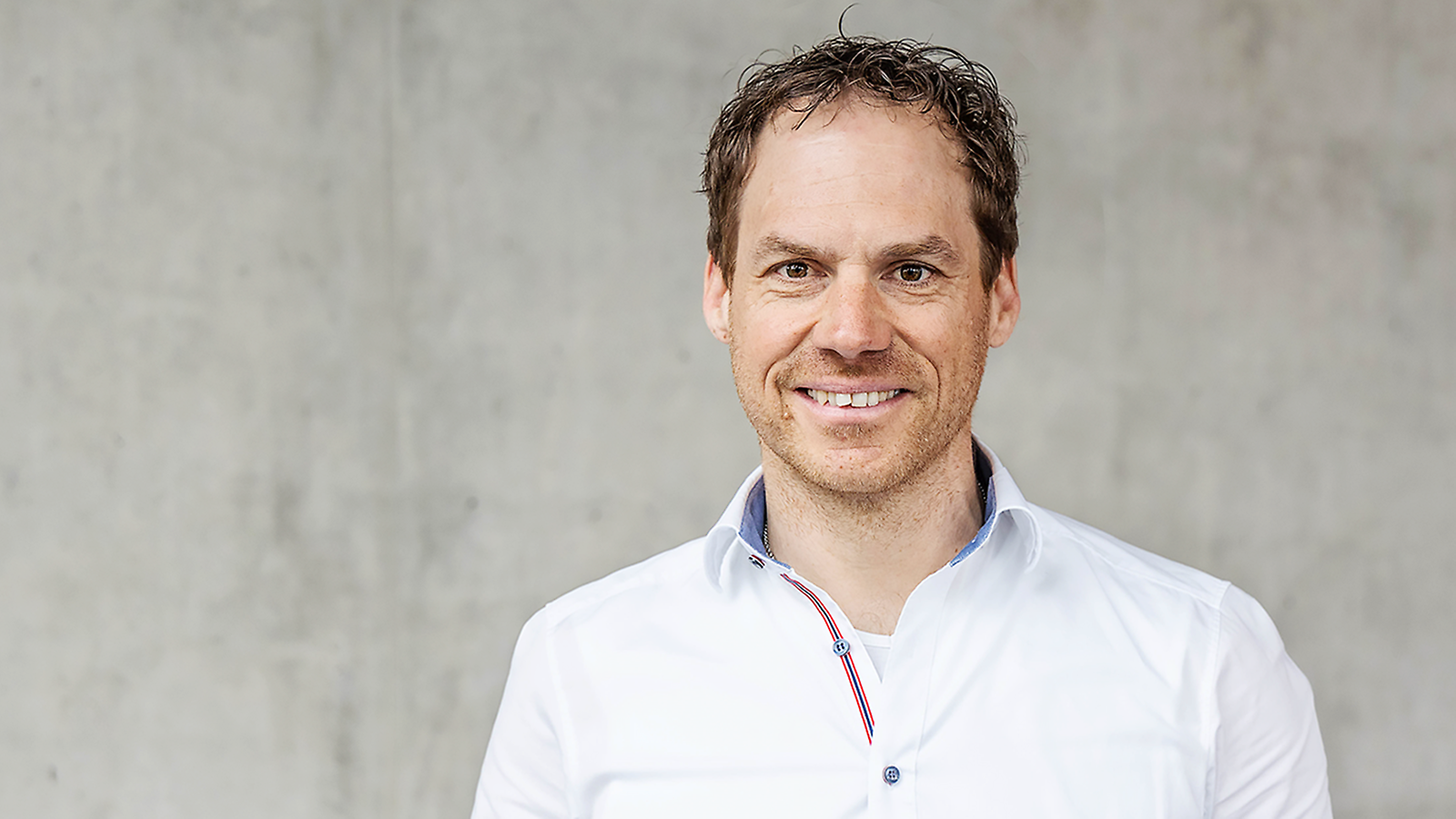
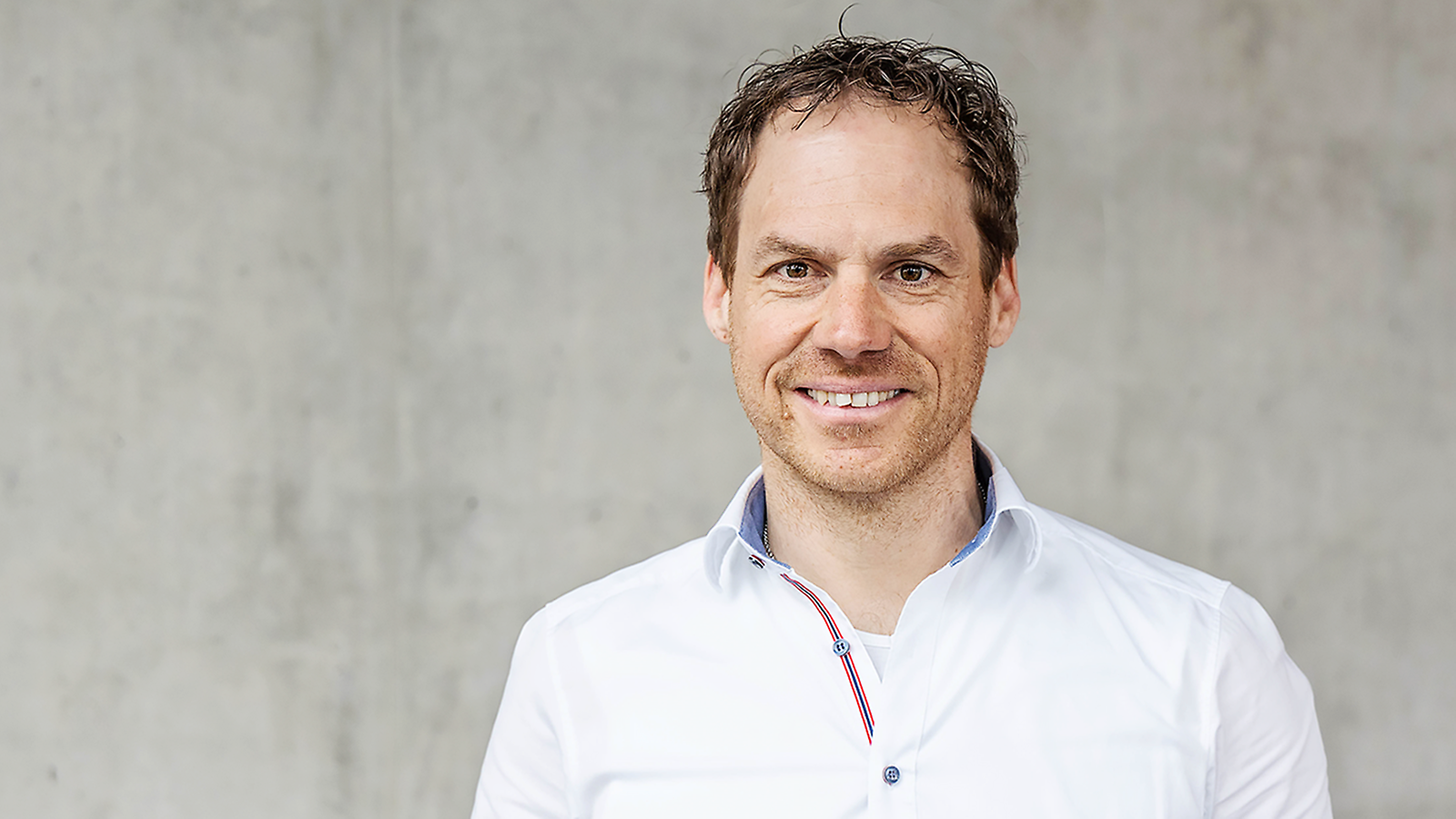
But it wasn't just the deformation that had to be taken into account - the scaffolding itself also had to adapt to these movements and the particularly complex pylon shape. Thanks to detailed structural calculations and intensive collaboration with the scaffolding department, the team was able to optimise the interaction of all components.’ Our tools help Martin to carry out the necessary structural calculations quickly and reliably. ‘For example, we use the PERI Force Control structural analysis programme. This allows us to transfer our planning from the CAD programme to the structural analysis software via an interface. This saves an enormous amount of time and helps us to develop even more precise solutions,’ explains Martin.
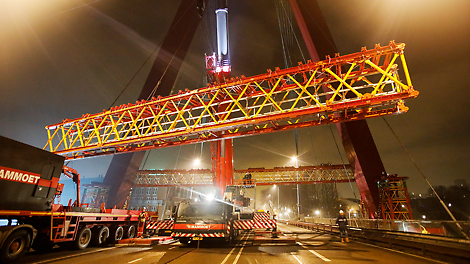
Detailed planning: How pre-assembled materials optimised the entire renovation process
In addition to precise calculations, safety on site was also of great importance. To protect the workers and motorists, Martin integrated a PERI UP working aisle into its truss girder solution. This allowed the site team to walk smoothly from one side of the road to the other while traffic continued to pass underneath. PERI's Dutch colleagues were on site to ensure that the access was installed correctly and safely and that any adjustments could be made quickly. They also took care of the logistics. As the bridge was only closed for a few hours at night, the material had to be delivered and installed with pinpoint accuracy. ‘Our colleagues therefore coordinated the truck loads. For example, pre-assembled truss girder units arrived, which not only reduced the assembly work, but also saved valuable time throughout the entire process,’ explains Martin.
What ultimately convinced Steigerbouw van der Panne to choose PERI was the comprehensive all-round package: from planning and structural calculations to logistics and personal on-site support, everything came from a single source. ‘With VARIOKIT and PERI UP, we offer a versatile system mix so that we are always able to find a suitable solution. Plus, all our systems are compatible with each other. This means that our clients don't have to work with several suppliers, which saves them a lot of time,’ says Martin. Thanks to this interaction and close coordination with our client, the renovation of the two pylons was completed in just three months. The project was such a highlight that we presented it at bauma 2019 on a large scale. And visitors can look forward to further exciting projects and live demos at bauma 2025.
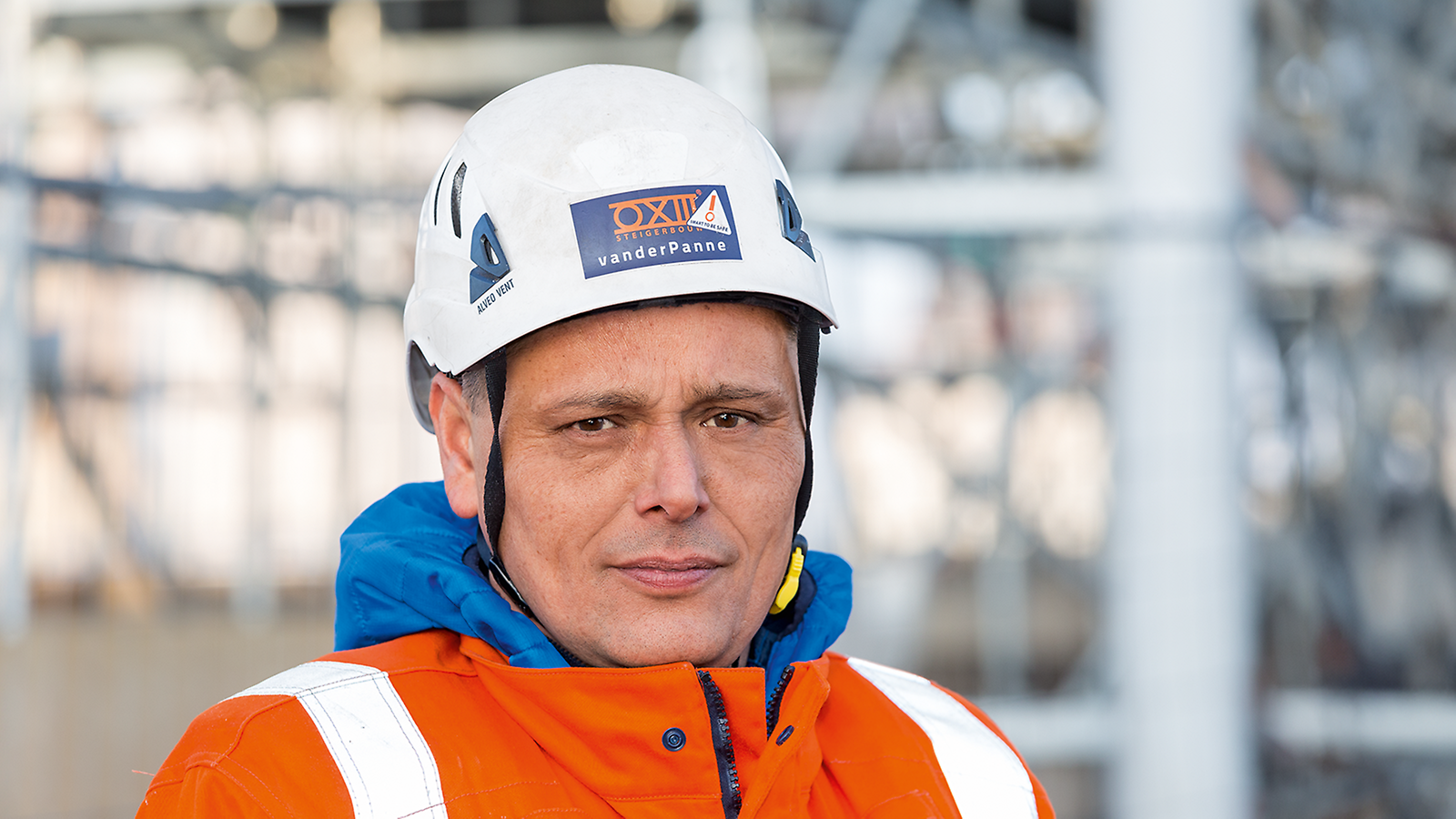
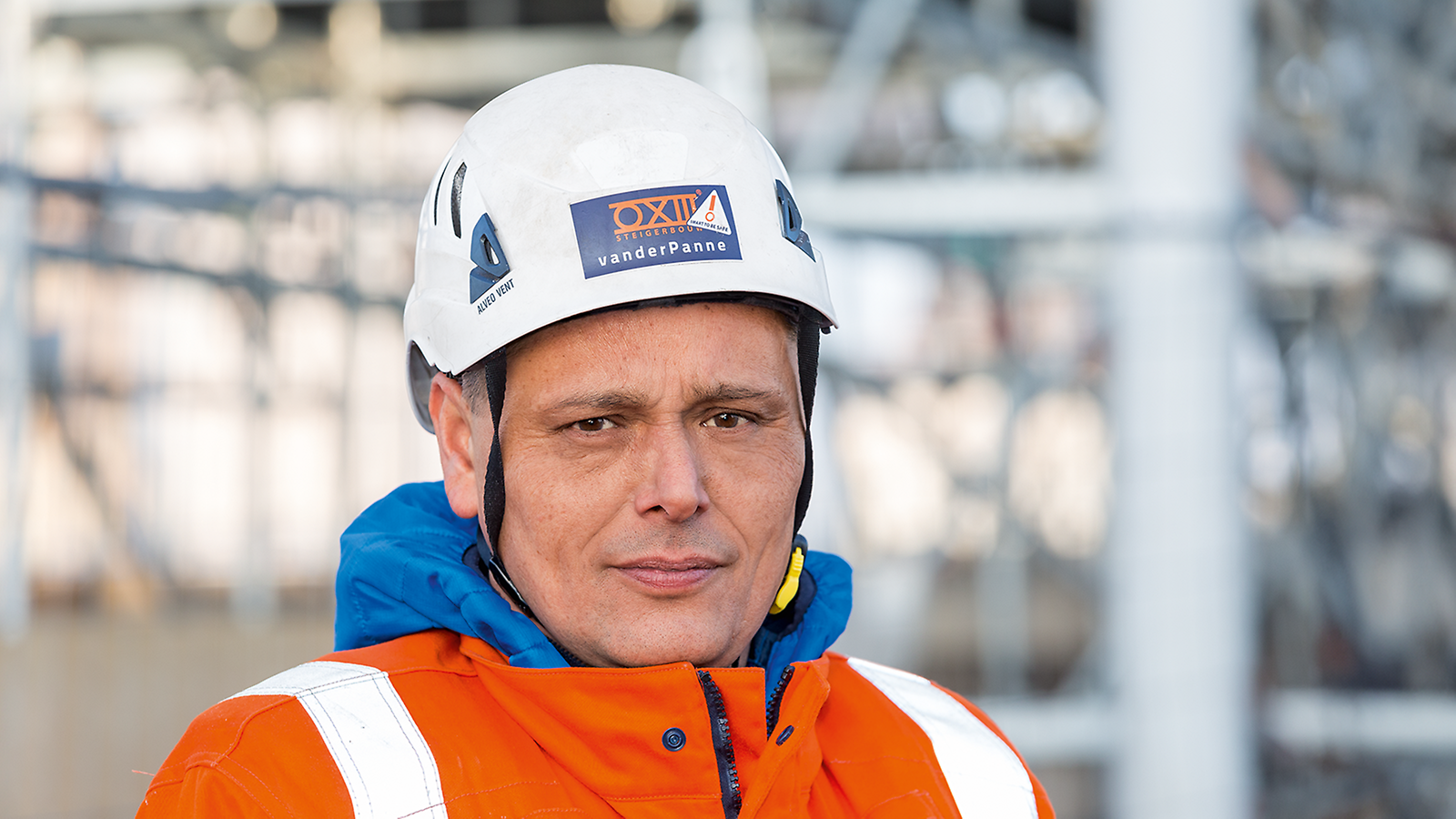
We are on site for you worldwide
Our support knows no borders - no matter where you are in the world. Simply select the website for your country and discover detailed information about our products, projects and contact details for our local contacts. We are always happy to assist you and look forward to helping you too.