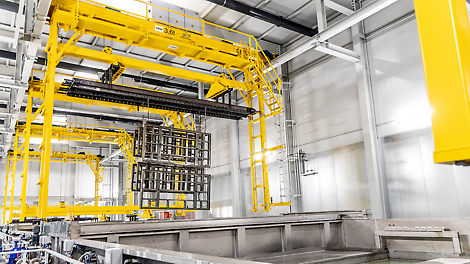
Setting clear goals and precise planning for our new coating factory
From the start in 2019 to the grand opening in summer 2024, Maximilian Rauner, Project Manager in Plant and Factory Planning, was among those involved in the realisation of our coating factory. For him, the project did not start with a symbolic ceremony. Instead, the first step was to optimise the planning. “The literal foundation consisted of clearly defined requirements for our core products. Our formwork elements needed to be even more resistant, more durable as well as more resource and cost-efficient,” describes Maximilian Rauner.
So, for our product managers, the first few weeks and months were all about finding the right technology for these challenges: “They evaluated, compared, evaluated, compared – and in the end, they found the right partner for our requirements,” says our Project Manager. It’s been a long-time companion of PERI: Chemetall, the global business unit for surface technology of BASF's Coatings division.
PERIskin saves energy: dip coating is done at only 20°C
Together with Chemetall, we have developed the PERIskin technology, in which the VIANT process plays a key role. The principle of this innovative method is special: the steel components are placed in a dip tank. There, the coating surrounds the components seamlessly and without gaps like a protective layer. This ensures that not only simple components but also complex metal parts are now coated and reliably protected against corrosion. “Another special feature is that the dip coating is done at just 20°C, so at room temperature. Unlike conventional coatings, which are applied at temperatures of up to 450°C, hardly any energy is required for our coating,” explains Maximilian Rauner passionately.
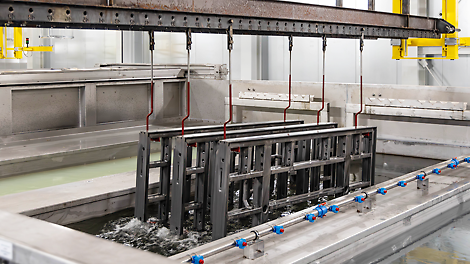
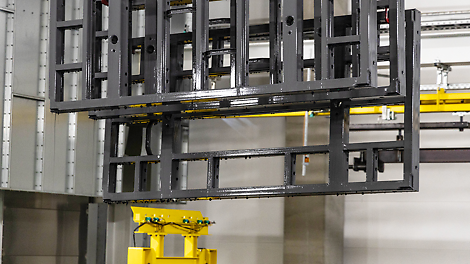
In addition to the low temperature, the new coating process can be combined with our powder coating, which brings further advantages. The concrete sticks less strongly to the components, so that the formwork elements are easier to clean. At the same time, all colour requirements are possible. “The advantages for our clients and ourselves are obvious: significantly more durable formwork and steel components, massive energy savings as well as lots of colour options,” summarises Maximilian Rauner.
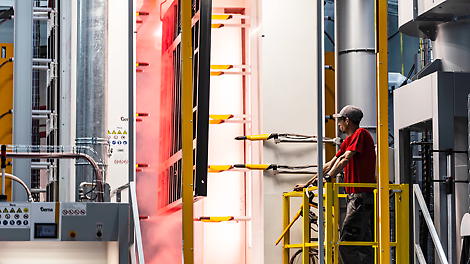
New factory for innovative coating process
To coat the large dimensions of the PERI components, 15 dip tanks with a volume of 55 m³ each were required. This represents around 300 bathtub fillings per tank. “Within our factory we created a coating lane on which large steel components are first cleaned and pickled and then coated with our new dip coating. In the next step they are baked, cooled and finally coated with powder coating,” says Maximilian Rauner.
During the last process, excess paint is extracted directly and fed back into the system cycle. This means that up to 98% of the paint that would otherwise not be used is reused.
Thanks to all these processes, the system consumes significantly less energy than similar methods. Plus, the factory's heat requirements can also be covered by our own biomass power plant.
Maximilian Rauner and our product managers are proud of this PERI project, which has also become a very special highlight for everyone involved. “We have invested in the future. That’s a big accomplishment. And in the medium term, our factory will probably be exciting for other industries as well,” says our Project Manager. Looking forward, PERI wants to offer the innovative coating process as a contract coating service.
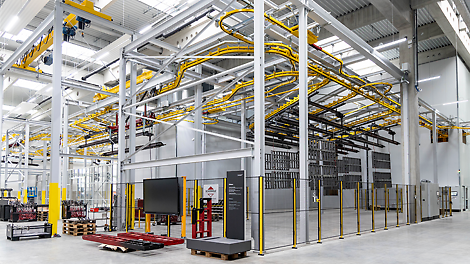
Moving forward together
Our Project Manager is more than satisfied with the result but is still mindful of the hurdles that presented the whole team with new challenges. “The hot phase of the construction work came at a time when the global market was struggling with a shortage of raw materials, supply bottlenecks and high prices,” he says, looking back. “We only mastered this because all the PERI departments involved worked together as a team.”
From Product Management to Plant and Factory Planning, Production, Construction and Building Management through to the Development department, everyone worked hand in hand to put the factory into operation in 2024.
We are on site for you worldwide
Our support knows no borders - no matter where you are in the world. Simply select the website for your country and discover detailed information about our products, projects and contact details for our local contacts. We are always happy to assist you and look forward to helping you too.